VT-447C Laminate/Prepreg
UL Approval: E214381 Version: 24/12/2024 /127/128/130Shelf life
Prepreg | Laminate | |||
---|---|---|---|---|
Storage Condition | Temperature | < 23℃ (73℉) | < 5℃ (41℉) | Room |
Relative Humidity | < 55% | / | / | |
Shelf Life | 3 Months | 6 Months | 24 Months |
Prepreg exceeding shelf life should be retested.
Precautions In Handling
- The prepreg exceeding shelf time should be retested.
- Take care in handling thin core laminates as they are easily damaged.
- If the prepreg is not consumed within 48hrs after opening the vacuum package, it is recommended that the bags be resealed.
- Material is available in both long and short grain. The grain direction is indicated on the label with an arrow.
Prepreg Availability
G/F Type | Resin Content | Press Thickness (mil) | Dk | Df | ||||||
---|---|---|---|---|---|---|---|---|---|---|
@ 1GHz | @ 2GHz | @ 5GHz | @ 10GHz | @ 1GHz | @ 2GHz | @ 5GHz | @ 10GHz | |||
7628 | 50% | 8.00 | 4.60 | 4.60 | 4.50 | 4.50 | 0.011 | 0.011 | 0.012 | 0.012 |
7628 | 46% | 7.50 | 4.60 | 4.60 | 4.50 | 4.50 | 0.011 | 0.011 | 0.012 | 0.012 |
2116 | 60% | 5.40 | 4.50 | 4.50 | 4.40 | 4.40 | 0.012 | 0.012 | 0.013 | 0.013 |
2116 | 58% | 5.00 | 4.50 | 4.50 | 4.40 | 4.40 | 0.012 | 0.012 | 0.013 | 0.013 |
1080 | 68% | 3.10 | 4.30 | 4.30 | 4.20 | 4.20 | 0.012 | 0.012 | 0.013 | 0.013 |
In order to satisfy CTI≥600V, 1 ply 2116 and 7628 or 2ply1080 is suggested to be used for outer layer. Remark: More types available upon request
Laminate Availablity
Core Thickness | Stack-up | Resin Content | DK | DF | |||||||
---|---|---|---|---|---|---|---|---|---|---|---|
mm | inches | @ 1GHz | @ 2GHz | @ 5GHz | @ 10GHz | @ 1GHz | @ 2GHz | @ 5GHz | @ 10GHz | ||
0.100 | 0.004 | 1-2113 | 57% | 4.50 | 4.50 | 4.40 | 4.40 | 0.012 | 0.012 | 0.013 | 0.013 |
0.125 | 0.005 | 1-2116 | 55% | 4.50 | 4.50 | 4.40 | 4.40 | 0.012 | 0.012 | 0.013 | 0.013 |
0.20 | 0.008 | 2-2113 | 57% | 4.50 | 4.50 | 4.40 | 4.40 | 0.012 | 0.012 | 0.013 | 0.013 |
0.20 | 0.008 | 1-7628 | 50% | 4.60 | 4.60 | 4.50 | 4.50 | 0.011 | 0.011 | 0.012 | 0.012 |
0.25 | 0.010 | 2-2116 | 55% | 4.50 | 4.50 | 4.40 | 4.40 | 0.012 | 0.012 | 0.013 | 0.013 |
0.30 | 0.012 | 2-1506 | 46% | 4.60 | 4.60 | 4.50 | 4.50 | 0.011 | 0.011 | 0.012 | 0.012 |
0.30 | 0.012 | 3-2113 | 57% | 4.50 | 4.50 | 4.40 | 4.40 | 0.012 | 0.012 | 0.013 | 0.013 |
0.38 | 0.015 | 2-7628 | 46% | 4.60 | 4.60 | 4.50 | 4.50 | 0.011 | 0.011 | 0.012 | 0.012 |
0.76 | 0.030 | 4-7628 | 46% | 4.60 | 4.60 | 4.50 | 4.50 | 0.011 | 0.011 | 0.012 | 0.012 |
1.50 | 0.060 | 8-7628 | 46% | 4.60 | 4.60 | 4.50 | 4.50 | 0.011 | 0.011 | 0.012 | 0.012 |
2.80 | 0.110 | 15-7628 | 46% | 4.60 | 4.60 | 4.50 | 4.50 | 0.011 | 0.011 | 0.012 | 0.012 |
Remark: 1) Copper foil: Hoz~6oz 2) More types available upon request 3) In order to satisfy CTI≥600V,please don’t design 0.10mm in outer layer
Baking Cycles During PCB Fabrication
There are a few baking cycles during PCB fabrication. Please take into consideration when appropriate.
Process | Purpose | Cycle |
---|---|---|
After Cutting (for thin core below 10 mil) | To get a stable dimension; To eliminate moisture | 2~4 hours @ 150ºC |
Before Drill | To get a stable dimension or full cure | 1 hour @ 150ºC |
Before HASL | To eliminate moisture | 2 hours @ 125ºC |
After Routing | To get a stable dimension | 1 hour @ 150ºC |
Before OSP | To prevent solder mask shelling | 1 hour @ 140ºC |
Before shipment (stored for over 3 months) | To eliminate moisture | 2~4 hours @ 105ºC |
- Dimension stability is the better than Standard FR4 material. - For unclad or single sided laminates to be used in multilayer, please brush unclad sides before use. - Please check with your oxide vendor to make sure that our material is suitable with your oxide process. We recommend to control the peel strength with brown oxide copper over 2 Lb/in. - After oxide, it is preferred to press them within 12 hours. Anyhow, not more than 24 hours.
Pressing
Item | Hot Start Press |
---|---|
Rate of Rise | ≥2.0ºC/min |
Cure Time | ≥185ºC 60~90min |
Max Temperature | 200~205ºC |
Full Pressure | ≥300 PSI |
Temperature to Apply Full Pressure Vacuuming should be continued until over 140ºC [Material Temperature] | ≤80ºC |
Typical Press Cycle
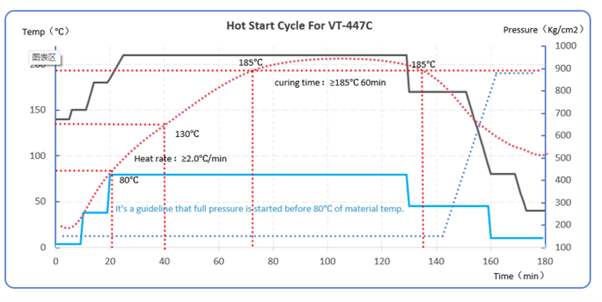
Typical Drilling Condition
Diameter | Stack Height | Spindle (KRPM) | Infeed (mm/s) | Retract (mm/s) | Hit Count |
---|---|---|---|---|---|
0.25mm | 1 PNL/Stack | 130 | 38 | 300 | 800 |
0.30mm | 1 PNL/Stack | 130 | 38 | 300 | 80 |
0.60mm | 1 PNL/Stack | 80 | 43 | 300 | 800 |
1. Excessive wear of carbide drill bits. Diamond coated drill bits preferred; 2. LE Aluminum sheet and white phenolic entry board are preferred;
Desmearing Process
The de-smearing rate of VT-447C is less than regular VT-447. 1 time vertical de-smearing is preferred. Please examine hole wall to check de-smearing effect. Typical de-smearing rate for reference only:1x De-smearing | Supplier | Chemical |
---|---|---|
0.27mg/cm2 | Atotech | Alkaline Permanganate |